Why scrap steel is the fastest route for steel's green transition
We have previously written about why high-quality scrap steel is necessary for the green transition. That piece mostly dealt with the quality and reliability advantages for the end users. But there are more advantages to scrap steel in relation to the green transition:
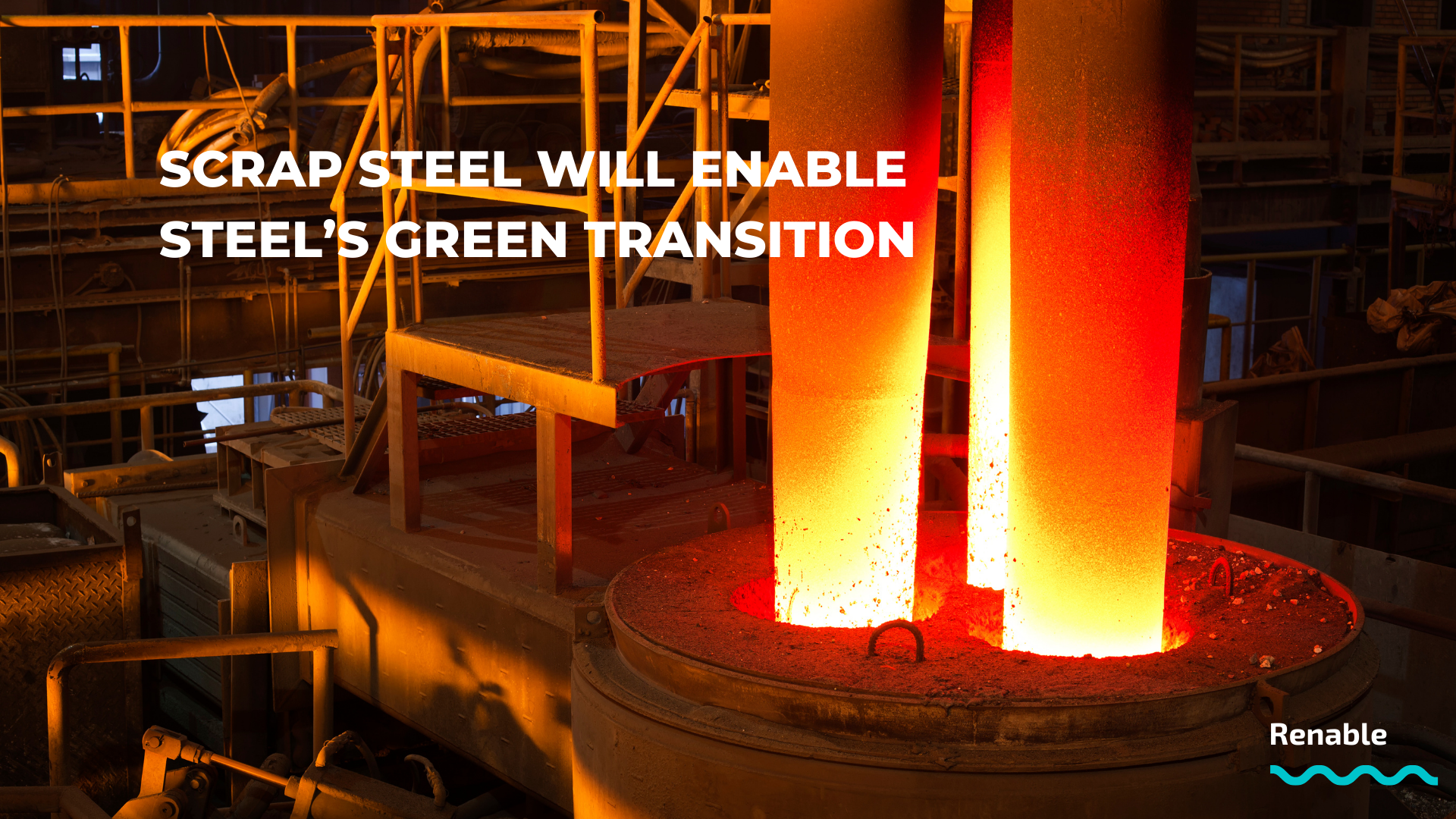
Primary (or "virgin") steel is made from iron ore, currently mostly through highly CO2-intensive Blast Furnace-Basic Oxygen Furnace (BF-BOF) processes. The two main contenders for decarbonising primary steel production are 1) clean hydrogen-based Direct Reduced Iron-Electric Arc Furnace (DRI-EAF) and 2) Carbon Capture Utilisation and Storage (CCUS). Of the two, DRI-EAF is both more technically and commercially developed, but CCUS is rapidly catching up.
According to the World Economic Forum, the DRI-EAF process using clean hydrogen has the potential to reduce emissions by up to 97%, but this comes with an expected "green" premium of 35-70% when compared to conventional BF-BOF processes. Further, constraints around the capacity of EAFs in comparison to larger blast furnaces and deployment at smaller facilities impact the applicability of this technology.
Again, according to the World Economic Forum, most CCUS-based technologies are not projected to become commercially available until after 2028. CCUS technologies have the potential to decrease emissions by up to 90% compared to BF-BOF. Bioenergy carbon capture and storage (BECCS), a modified CCUS technology, can achieve up to negative emissions from BF-BOF, though results are dependent on the source of bioenergy. Irrespective of exact technology, all CCUS technologies entail a significant green premium in the range of 65-120%. Although DRI-EAF with CCUS is technically feasible, its carbon capture efficiency would be limited, because the CO2 concentration in the exhaust gases are low. Therefore, CCUS technology is most suited for decarbonizing BF-BOF assets, given the higher concentration of CO2 in blast furnace gases.
For secondary (i.e. scrap) steel decarbonization, EAF-based production using 100% renewable electricity is a mature and available technology. The World Economic Forum estimates that EAF technology can reduce emissions by 90-95% compared to BF-BOF, with only a marginal cost premium of 8-13%. While there are limitations for the use of scrap due to variance in the quality of the scrap, using maritime steel scrap would go a long way towards addressing those limitations, as previously argued.
If we look at other industries than the steel industry, numbers whispered to us indicate that pioneering end customers are prepared to pay 4-30% more for carbon-reduced goods or services. The additional cost of carbon-reduced steel made using high-quality scrap and renewable electricity-driven EAFs seems thus to be well within the pain threshold of first-mover customers, and thus the obvious choice to begin seriously decarbonising the steel industry.
That is of course not enough. Global steel demand is projected to be rather higher than the amount of steel that can be circulated back into the economy, so for the foreseeable future there will be a need for primary steel. As indicated by the World Economic Forum, the commercial and technical competitiveness of technologies for decarbonising primary steel production may be a bit into the future, and hence, there is a need for a real-world, realistic classification tool for evaluating just how "green" a given steel production facility is within its category. Unsurprisingly, steel scrap plays a role in just such a tool, proposed by the German Wirtschaftsvereinigung Stahl. The tool proposes to evaluate production using the two axes of embedded emissions and percentage of scrap used. Production is then placed on a sliding scale as follows:
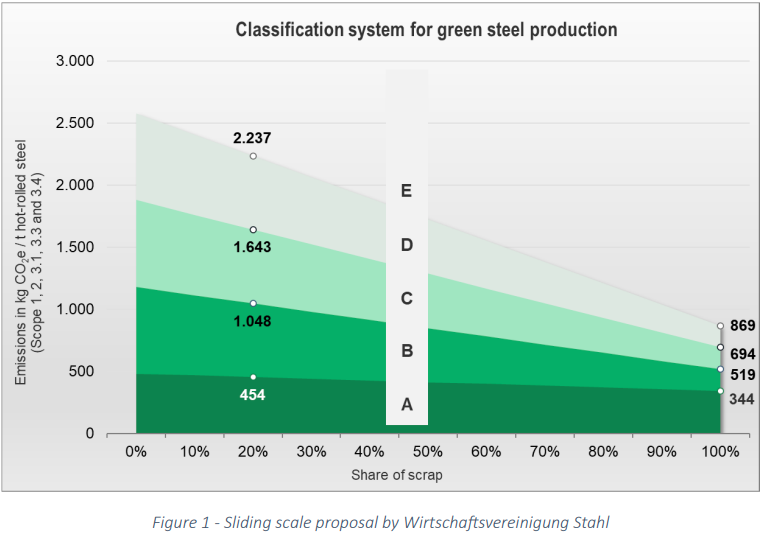
We think this is an excellent proposal, emphasising the importance of scrap use, while allowing the industry to compare itself within its categories, and would be happy if this tool was adopted for purposes of being able to make "green claims" for the industry.